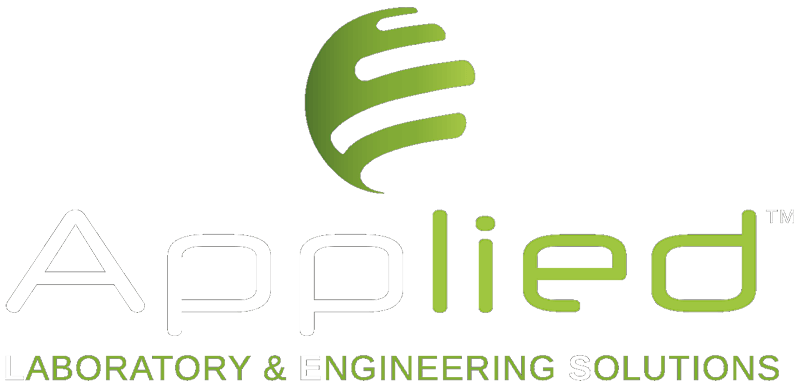
10, Agion Anargiron Str.
Marousi Attica, 151 24
Greece
The selection of appropriate equipment is perhaps the most important part of designing a complete solution for a metallographic sample preparation task aimed at observing the microstructure using an optical, inverted metallographic, or scanning electron microscope.
Our company, taking into account all the specific details of each application, recommends the suitable equipment and consumables to achieve the best possible result. Recently, we have completed the installation of the following machines.
Installed Equipment:
As part of the comprehensive solutions we strive to offer, we have recently installed the QCUT 250M cutting machine by QATM Germany for transverse cutting of copper alloy samples. We have also successfully proposed and implemented cuts using a special consumable corundum cutting disc suitable for non-ferrous metals, especially copper.
Subsequently, we recommended the placement of smaller, thin samples in a precision microtome, QCUT 150A, which has been also installed successfully. This machine allows for automatic cutting with controlled feed and force using a special silicon carbide cutting disc, specifically designed for cutting non-ferrous materials and especially copper alloys.
In the first case of metallographic cutting done on the QCUT 250M tabletop cutting machine, the cutting techniques are manual, and the user's handling is crucial during both the sample securing stage and the cut-off wheel lowering stage to perform the metallographic cut. A key requirement is the firm clamping of the samples in a suitable vice or holder to prevent movement, slipping, or intense vibration during cutting.
In the second case of cutting, which is done automatically on the QCUT 150A microtome, the selection of cutting speed, feed, and force plays a particularly important role in producing deformation free surfaces. A surface is considered perfect after cutting when it is smooth, free of large cracks, and reflects light uniformly without showing poor flatness, which would be indicated by the formation of multiple layers. We normally recommend the cutting speed based on the sample dimensions and hardness (HV – Vickers).
For copper samples, when a vacuum mounting system (Infiltration Unit) is available, and depending on the shape, dimensions, and the alloy itself, it is appropriate to mount them either with suitable epoxy resins under vacuum or, for speed and adhesion purposes, with fast-curing acrylic resins. Polypropylene or polyethylene molds should be used depending on the chosen resin. These methods were successfully tested.
Regarding the grinding/polishing of copper alloys that are sensitive to scratches, the appropriate method is selected based on the hardness and ductility of each alloy. This method is customized according to the application’s particularities. Our goal is to ensure that the proposed methods do not exceed four stages, and the preparation times for each step are always shorter than those of competing methods.
Optimal polishing occurs in two stages, and etching can be either chemical or electrolytic (QETCH 1000), depending on the application and whether fast results are required. In such cases, using the appropriate electrolyte is essential. The electrolytic etching and polishing curve defines the optimal conditions/parameters that should be selected on the QETCH 1000 machine.
Contact us, share the details of your application, and we will be happy to prepare a grinding/polishing method tailored to your needs, depending on the type of observation you will conduct on the prepared surfaces (observation via optical microscope or scanning electron microscope).
10, Agion Anargiron Str.
Marousi Attica, 151 24
Greece
Η Διοίκηση της Applied Laboratory & Engineering Solutions έχει καθορίσει και τεκμηριώσει την πολιτική της για την ποιότητα, βασισμένη στην εφαρμογή Συστήματος Διαχείρισης Ποιότητας κατά το διεθνές πρότυπο ISO 9001:2015 για τη δραστηριότητα της:
ΕΜΠΟΡΙΑ ΕΠΙΣΤΗΜΟΝΙΚΩΝ ΟΡΓΑΝΩΝ ΚΑΙ ΕΞΟΠΛΙΣΜΟΥ
Η Διοίκηση εξασφαλίζει ότι αυτή η Πολιτική Ποιότητας είναι κατανοητή, εφαρμόζεται και διατηρείται σε όλα τα επίπεδα.
Όραμα της Επιχείρησης είναι η αύξηση του μεριδίου της αγοράς και η ισχυροποίηση της ανταγωνιστικότητάς της προσφέροντας υψηλής ποιότητας προϊόντα.
Φιλοσοφία της Applied Laboratory & Engineering Solutions είναι:
Γενικές κατευθυντήριες οδηγίες:
Αθήνα, 12 – 09 – 2022
Η Γενική Διευθύντρια
Μαρία Λογοθέτη
The Management of Applied Laboratory & Engineering Solutions has defined and documented its quality policy, based on the implementation of a Quality Management System according to the international standard ISO 9001:2015 for its activities:
TRADE OF SCIENTIFIC INSTRUMENTS AND EQUIPMENT
Management ensures that this Quality Policy is understood, applied, and maintained at all levels.
The company’s vision is to increase its market share and strengthen its competitiveness by offering high-quality products.
The philosophy of Applied Laboratory & Engineering Solutions is:
General Guidelines:
Athens, 12 – 09 – 2022
The Director
Maria Logotheti